An electric concrete pump is a crucial piece of equipment used in construction projects to transport liquid concrete to designated locations efficiently and with minimal labor. Unlike diesel-powered pumps, electric concrete pumps are known for their cleaner, quieter operation, making them ideal for projects with nearby residential areas or indoor settings. They are also highly efficient and reliable, provided they are maintained properly. Regular and meticulous maintenance ensures the longevity of the equipment, reduces downtime, and minimizes the risk of malfunctions that can lead to project delays.
In this passage, we will cover the essential tips for maintaining an electric concrete pump, with a focus on keeping it running smoothly, extending its operational life, and ensuring safety during use.
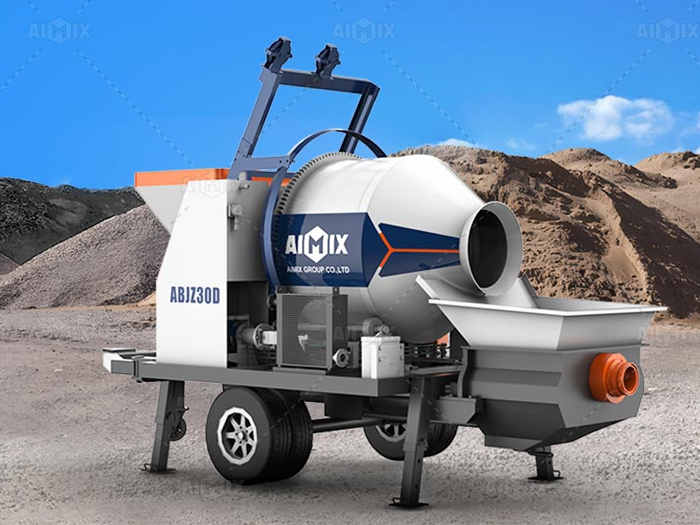
Regular Cleaning After Use
One of the most fundamental maintenance tasks for an electric concrete pump is regular cleaning after each use. Concrete tends to harden quickly, and any residual material left in the pump’s components can lead to blockages, reduced efficiency, or even damage over time.
a. Cleaning the Hopper
The hopper is the part of the pump where the wet concrete is initially loaded. After the job is finished, you must clean out the hopper thoroughly to prevent leftover concrete from hardening. Use water and a scrub brush to remove any residual concrete from the walls and bottom of the hopper. Make sure no concrete is left sticking to the sides.
b. Flushing the Pipes and Hoses
After the hopper is cleaned, flush the pump’s pipes and hoses with water to remove any remaining concrete. Many electric concrete pumps come with an automated flushing system, which makes this process easier. If your pump doesn’t have one, you can manually flush the system by circulating water through the pipes and hoses under low pressure until all debris is removed. Ensure that no concrete hardens in the pipes, as blockages can be difficult to clear and may cause permanent damage.
c. Cleaning the Pumping Mechanism
The pumping mechanism, which is powered by the electric motor, should also be cleaned thoroughly. Make sure that any part of the pump that comes into contact with the concrete is cleaned. Pay attention to the valves and cylinders, as leftover concrete in these areas can affect the pump’s ability to function smoothly.
Lubrication of Moving Parts
Proper lubrication is crucial to maintaining the smooth operation of your electric concrete pump. Moving parts such as pistons, valves, bearings, and cylinders are under constant stress while the pump is in operation, and without proper lubrication, friction can cause wear and tear.
a. Lubricate the Pistons and Valves
The pistons and valves are vital to the concrete pumping mechanism. Regular lubrication helps reduce friction and wear, which in turn enhances the pump’s efficiency and longevity. Use a high-quality lubricant or grease that is recommended by the pump’s manufacturer like Aimix, and apply it to the pistons and valves as specified in the maintenance manual. The frequency of lubrication may vary based on how often the pump is used, but it’s generally a good practice to lubricate these parts after every few uses.
b. Grease the Bearings and Rotating Components
The electric concrete pump’s bearings and rotating components must also be properly greased to ensure they can handle the high loads during operation. Neglecting to grease these parts can lead to increased friction, overheating, and eventually component failure. Inspect the pump’s bearings regularly and apply grease as needed.
c. Check the Hydraulic System
Most electric concrete pumps rely on a hydraulic system to power the pumping mechanism. The hydraulic fluid must be kept at the appropriate level, and it’s essential to check the system for leaks regularly. Over time, hydraulic fluid can become contaminated or degrade, so follow the concrete pump manufacturer’s guidelines for when to replace it.
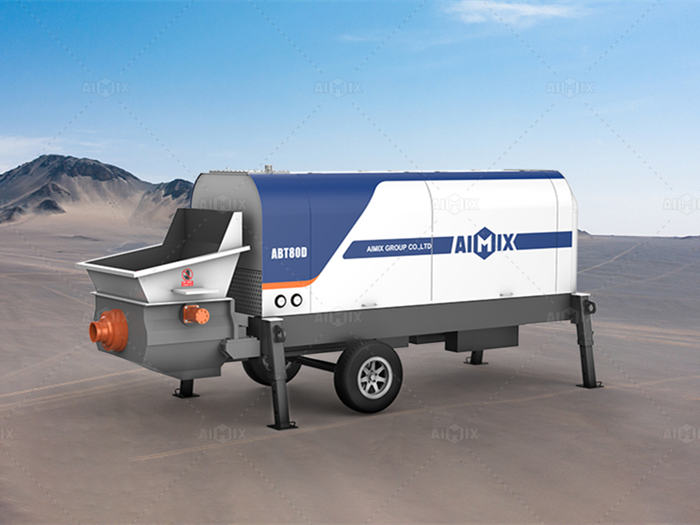
Inspection of Electrical Components
An electric concrete pump relies on a motor powered by electricity, so it’s essential to regularly inspect the pump’s electrical components. Any failure in the electrical system can cause the pump to malfunction or stop working altogether.
a. Inspect the Power Supply and Cables
One of the most common issues with electric concrete pumps involves problems with the power supply or cables. Regularly check the power cord and connections for signs of wear, fraying, or damage. Ensure that the plug and socket are in good condition and that there are no exposed wires. Damaged cables should be replaced immediately to prevent electrical hazards.
b. Monitor the Electric Motor
The electric motor is the heart of the pump, so it’s critical to monitor its performance regularly. Listen for unusual noises, such as grinding or whining sounds, which could indicate motor issues. Additionally, check the motor’s temperature while it’s operating. Overheating could signal problems such as excessive load or poor ventilation. If you notice any irregularities in the motor’s performance, it’s advisable to have it checked by a professional technician.
c. Test the Control Panel and Switches
The control panel allows operators to start, stop, and adjust the pump’s settings. Regularly test the switches, buttons, and control panel to ensure they are functioning properly. Any delay or malfunction in the controls could be an early warning sign of electrical problems. Keep the control panel clean and dry, as moisture can cause short circuits or malfunctions.
Regular Inspection of Wear Parts
Over time, certain parts of an electric concrete pump are more susceptible to wear and tear due to their direct contact with the concrete or frequent movement. Monitoring the condition of these parts is crucial to preventing breakdowns.
a. Check the Wear Plates and Cutting Ring
The wear plates and cutting ring in an electric concrete pump are constantly exposed to the abrasive nature of the concrete mix. Inspect these parts regularly for signs of wear, such as thinning or chipping. Replace worn-out wear plates and cutting rings promptly to avoid damaging other components of the pump.
b. Monitor the Condition of Seals and Gaskets
Seals and gaskets are essential for keeping concrete and hydraulic fluid contained within the pump. Over time, seals can degrade or crack, leading to leaks. Check all seals and gaskets for signs of wear, and replace them as needed. Leaky seals not only affect the pump’s performance but can also cause messes and pose safety hazards.
Routine Maintenance Schedule
Creating and adhering to a routine maintenance schedule is the best way to ensure your electric concrete pump remains in good working condition. A detailed maintenance log should be kept, tracking every inspection, cleaning, lubrication, and part replacement. Here’s a basic schedule to follow:
Daily Maintenance: Clean the pump thoroughly after each use, inspect the hoses and pipes, and check the control panel for proper operation.
Weekly Maintenance: Lubricate the pistons, valves, and bearings, and check the power cables and hydraulic fluid levels.
Monthly Maintenance: Inspect the wear parts such as wear plates, cutting rings, and seals, and monitor the condition of the motor and electrical components.
Seasonal Maintenance: Perform a thorough inspection of the entire pump system, replace any worn or damaged parts, and recalibrate the control settings if necessary.
Proper Storage
When the electric concrete pump is not in use, it’s important to store it properly to prevent damage from environmental factors. Always store the pump in a clean, dry area, away from moisture and extreme temperatures. If the pump will be out of use for an extended period, cover it to prevent dust buildup and ensure that all moving parts are well-lubricated before storage.
Maintaining an electric concrete pump is essential for ensuring its long-term performance, safety, and reliability. By regularly cleaning the pump, lubricating moving parts, inspecting electrical components, monitoring wear parts, following a maintenance schedule, and properly storing the pump when not in use, you can minimize the risk of breakdowns and costly repairs. Proper care and maintenance will not only keep the pump in optimal condition but also help you avoid project delays and safety hazards on the job site.