Preparing and maintaining the rail of a rail mounted gantry crane (RMG) is crucial for ensuring smooth and efficient operations in container terminals and port facilities. The rail system serves as the foundation for the crane’s movement, supporting heavy loads and facilitating precise container handling. Proper preparation and maintenance of the rail are essential to prevent accidents, minimize downtime, and prolong the lifespan of the gantry crane. Below are comprehensive guidelines and best practices for preparing and maintaining the rail of an rail mounted gantry crane:
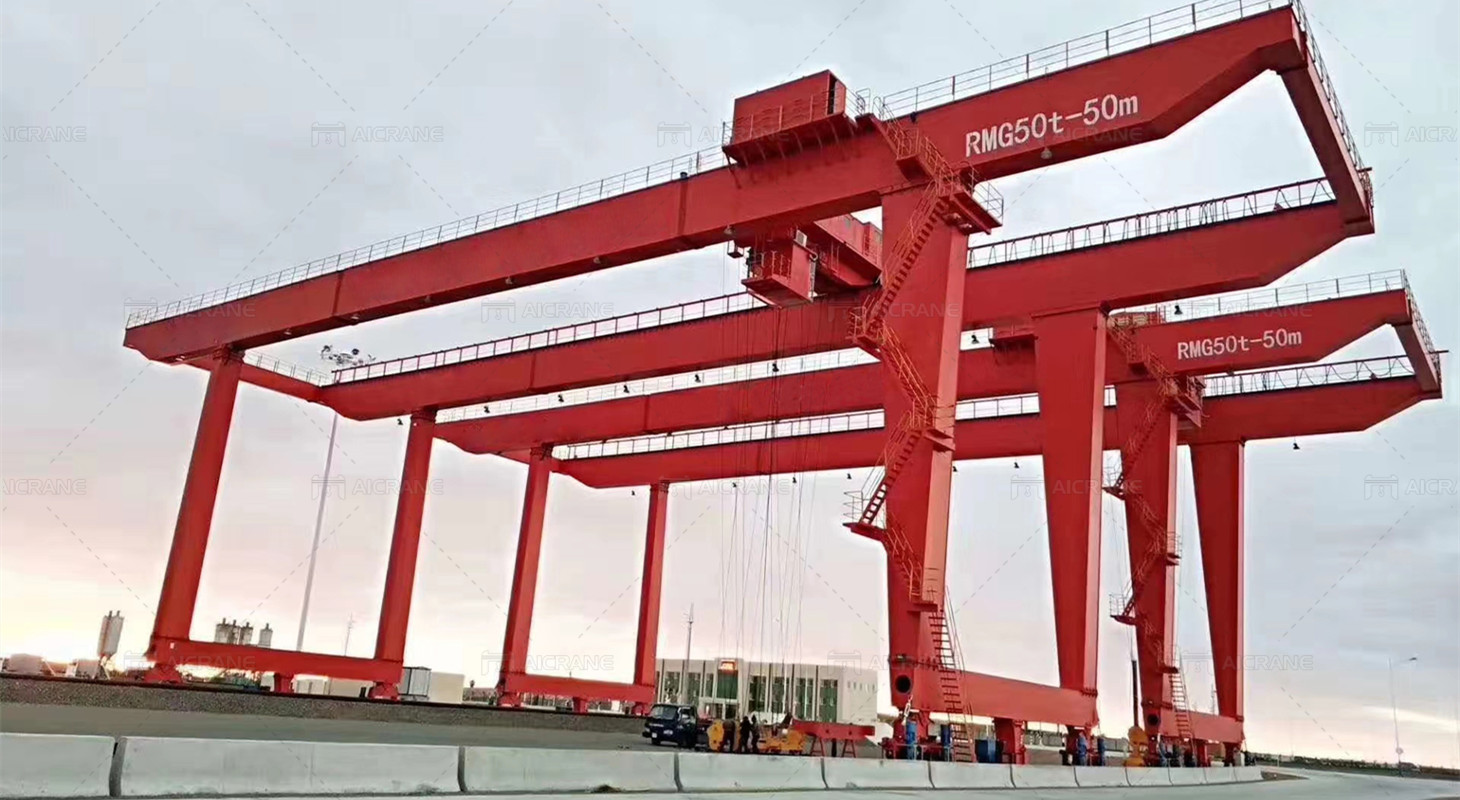
Preparation Before Installation
Site Inspection Conduct a thorough site inspection to assess the ground conditions, track alignment, and foundation requirements for installing the rail. Ensure the site is level, compacted, and free from debris or obstacles that may impede rail installation or crane operation.
Rail Specification Select high-quality rails and rail components suitable for rail mounted gantry crane operations. Consider factors such as rail type (e.g., A55, A65 rails), rail profile, gauge, rail fastenings, joint bars, and rail pad materials. Verify that the rail specifications meet industry standards and crane manufacturer requirements.
Alignment and Leveling Use precision tools and techniques to align and level the rail tracks accurately. Proper alignment ensures smooth movement of the rail mounted gantry crane along the rail tracks without binding, excessive wear, or misalignment issues. Verify the rail gauge and track geometry according to design specifications.
Installation Procedures
Rail Installation Follow the crane manufacturer’s installation guidelines and procedures for installing the rail tracks. Use specialized equipment such as rail cranes, rail aligners, and track jacks to position and secure the rails. Ensure proper rail fastenings, bolt torques, and joint connections to maintain structural integrity.
Rail Welding If required, perform rail welding using qualified welders and welding procedures. Conduct non-destructive testing (NDT) of rail welds to verify weld quality, integrity, and compliance with welding standards. Ensure proper rail expansion joints and thermal stress considerations to prevent rail buckling or distortion.
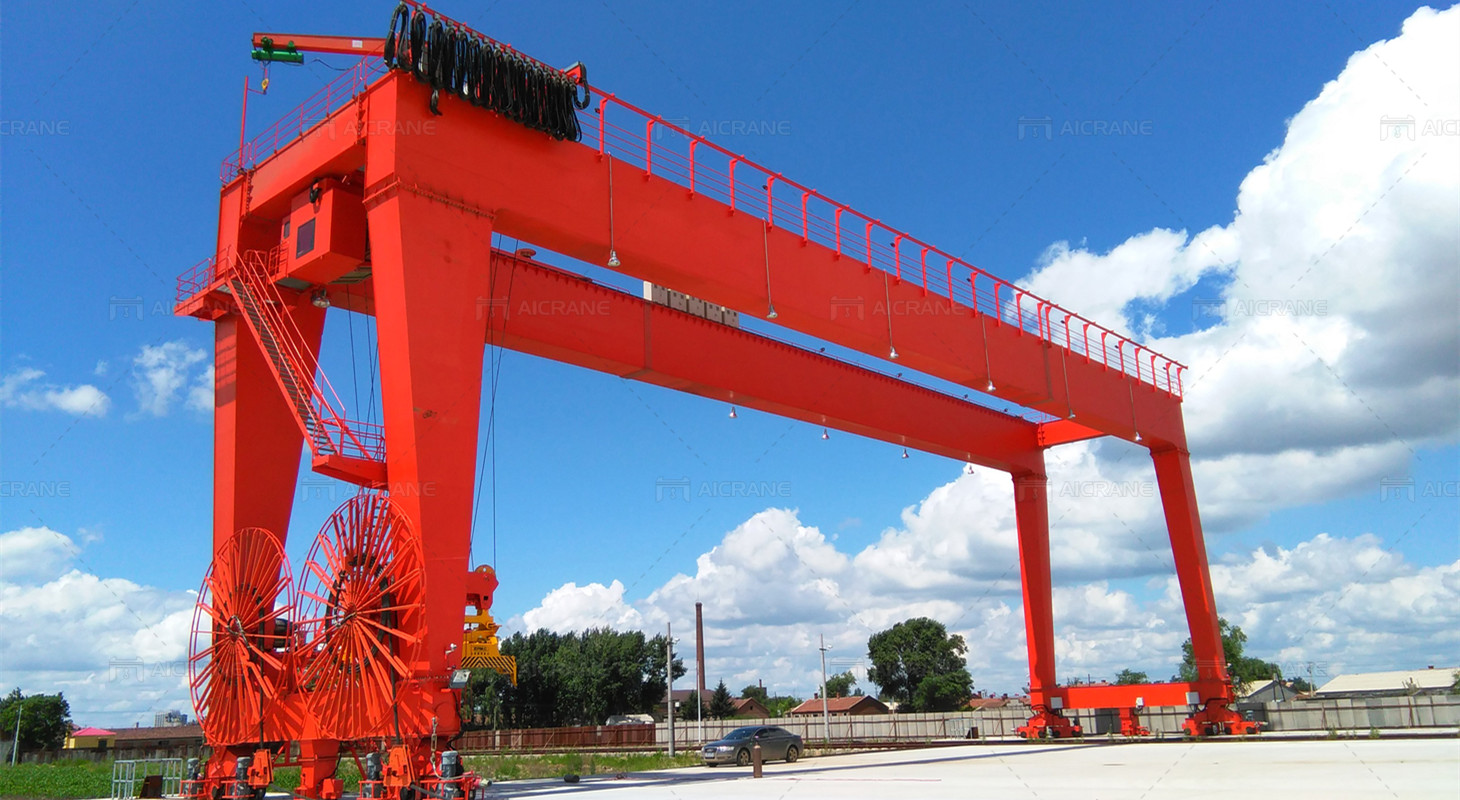
Ongoing Maintenance Practices
Regular Inspections Implement a scheduled inspection program to assess the condition of the rail tracks, rail fastenings, welds, joint bars, and rail pad conditions. Inspect for signs of wear, corrosion, cracks, rail misalignment, loose bolts, or damaged components that may affect rail stability or crane operation.
Rail Lubrication Apply appropriate rail lubricants to reduce friction, wear, and noise during crane movement. Lubricate rail-wheel interfaces, guide rollers, and rail contact surfaces to ensure smooth and efficient crane travel along the tracks. Use automated lubrication systems or manual lubrication methods as recommended by the crane manufacturer.
Track Cleaning: Regularly clean the rail tracks and rail surfaces to remove dirt, debris, rust, and contaminants that can impair crane movement or cause premature wear. Use track cleaning equipment, brushes, or compressed air to maintain clean and smooth rail surfaces.
Tensioning: and Fastening Periodically check and adjust rail fastenings, bolts, and joint connections to maintain proper tension, alignment, and structural stability. Use torque wrenches or tensioning tools to ensure optimal rail fastening and prevent loosening or rail movement.
Corrosion Protection: Apply corrosion-resistant coatings or paint to protect rail surfaces from corrosion, rust, and environmental exposure. Inspect rail coatings regularly and touch up any damaged or worn areas to maintain protective integrity.
Track Alignment and Geometry: Conduct periodic track alignment checks and geometric surveys to verify rail alignment, gauge, curvature, and vertical profile. Address any track irregularities or deviations promptly to prevent crane operational issues or rail track damage.
Safety Measures and Compliance
Safety Barriers Install safety barriers, guardrails, or fencing along rail tracks to prevent unauthorized access, reduce collision risks, and enhance worker safety. Ensure clear signage, markings, and warning signals for crane operators and personnel working near rail tracks.
Emergency Procedures: Develop and communicate emergency procedures for rail-related incidents, derailments, or track obstructions. Train crane operators and maintenance personnel on emergency response protocols, including shutdown procedures, evacuation routes, and communication protocols.
Regulatory Compliance: Adhere to industry regulations, safety standards, and crane manufacturer recommendations for rail mounted gantry crane operations, maintenance, and safety practices. Conduct regular audits, safety assessments, and compliance checks to ensure adherence to legal requirements and best practices.
By following these comprehensive preparation and maintenance guidelines, you can ensure the optimal performance, safety, and longevity of the rail mounted gantry crane rail system in container terminals and port facilities. Prioritize proactive maintenance, regular inspections, lubrication, cleaning, alignment checks, and safety measures to maximize crane efficiency and minimize downtime or safety risks associated with rail operations. Collaboration between crane operators, maintenance teams, and safety personnel is essential for maintaining a reliable and safe rail system for RMG crane operations.